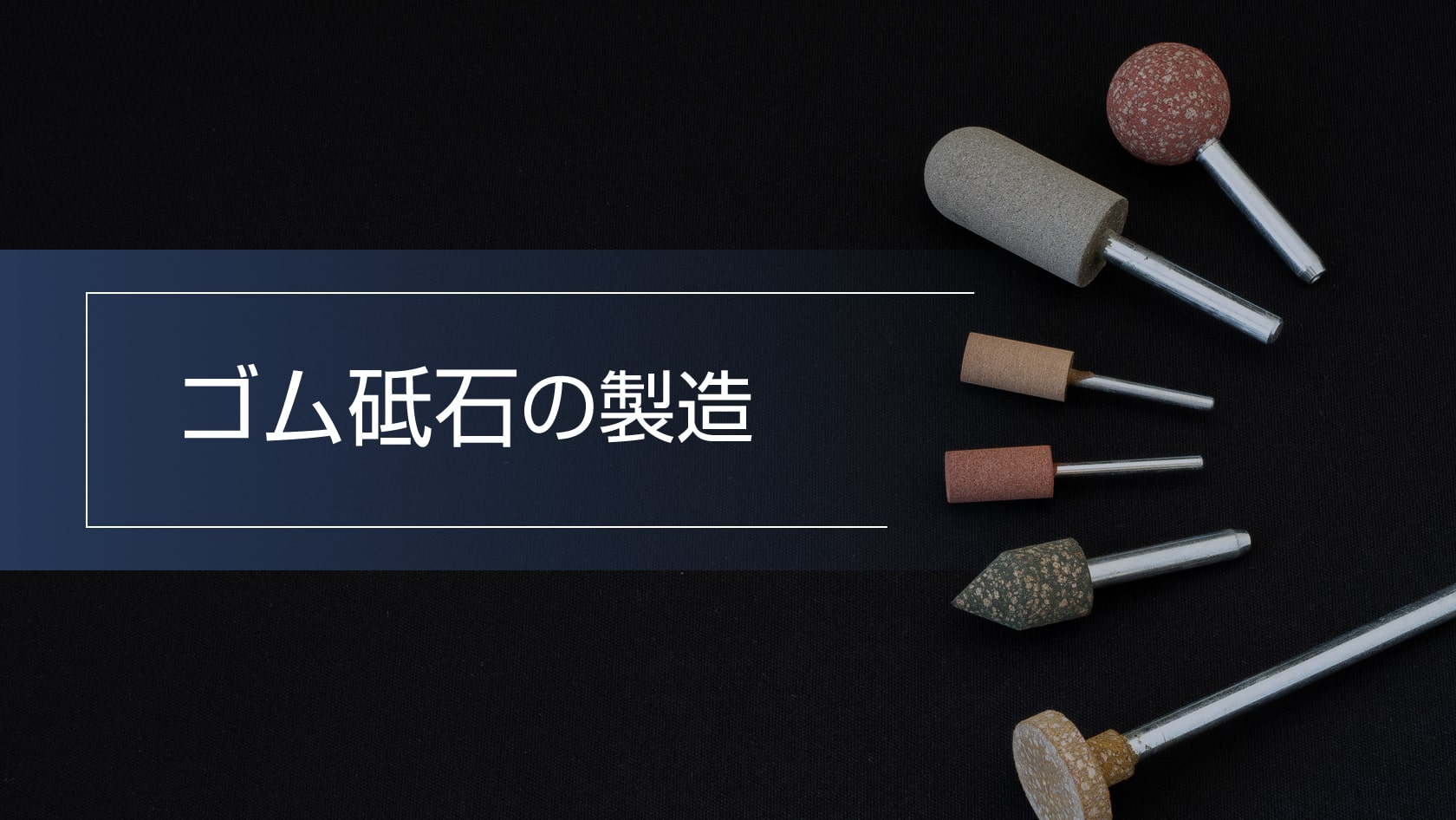
ゴム砥石の製造は、大きく分けて「練り工程」→「プレス工程」→「ドレス工程」の3つの工程に分かれます。
ここでは、ゴム砥石製造の各工程について解説します。
① 練り工程
練り工程では、専用のオープンロール機を使用して、素材となるゴムを加工します。
この機械は、2本の金属ロールが対向して回転することで、ゴムをすり潰し、薬品や砥粒(砥石の素材)を均一に混ぜ込むことができます。
素練り作業ではポリマー(原料ゴム)のみを練ります。
ポリマーに剪断力(せんだんりょく)を加えることで分子同士の結合が崩れ、ゴム全体が柔らかくなり、後の作業がしやすくなります。
素練りで柔らかくなったポリマーに、必要な薬品や砥粒(砥石の素材)を加えるのが混練りです。
薬品や砥粒の量、投入のタイミング、練り方によって製品の性能が大きく変わるため、経験豊富なゴム練り技術者による正確な作業が求められます。
混練り作業の完了後、ゴムを必要な厚さや大きさに切断する分出し作業が行われます。
② プレス工程
ゴムの成形には直圧成形、注入成形、射出成型などの方法がありますが、ゴム砥石の製造では主に直圧成形で製作されます。
直圧成形では、ホットプレスと呼ばれる、熱と圧力を同時に掛ける事が出来る油圧プレス機を用いて、分出しされたゴム材料を直接金型に仕込み、一定時間、圧力と熱を掛けてゴムを反応させ、必要な形を成形します。
素材ゴムの違いや製品の大きさ、重量、必要な性能に合わせて、圧力、温度、時間、投入ゴム量などを細かく調整します。積み重ねられた経験とノウハウが物を言う、非常に重要な作業です。
③ ドレス工程
ドレッシングマシンと呼ばれる専用の加工機を用いて、プレス成型されたゴム砥石を削って加工し、製品として必要な寸法や形状に整えます。
プレス成型されたゴム砥石は、回転バランスがしっかり取れておらず、そのままでは砥石として使う事ができません。
また、用途に応じて先端を尖らせたり、側面を丸くする等、お客様の要望に応じて形を変える必要もあります。
そこでドレッシングマシンを使ってゴム砥石を削り、所定の寸法・精度に加工を行います。
当社では、画像寸法測定器や3D形状測定器を使用して、製品が所定の寸法・形状に加工されているかを確認しています。